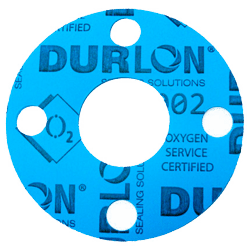
Durlon 9002
Durlon 9002 is an adaptation of the original glass-filled formula to better meet extreme cryogenic system demands.
Durlon 9002 has passed both gaseous, [up to 260°C (500°F) and 52 bar (754 psi)] and liquid oxygen tests performed by BAM Federal Institute of Materials Research and Testing.
Durlon 9002 has also been tested for LOX Mechanical Impact Sensitivity (ASTM G86 & ISO 21010), passing with zero reactions out of twenty tests (0/20) at a test reaction frequency of 0%.
Durlon 9002 is readily available through the standard manufacturing process and requires no secondary heat or cleansing treatments prior to gasket cutting. Once gaskets are cut, traditional oxygen cleaning standards must be applied for safety.
Durlon 9002 comes available as oxygen cleaned gaskets, bagged, labelled, and sealed according to the European Industrial Gases Association standard for Cleaning of Equipment for Oxygen Service.
Durlon 9002 has achieved numerous certifications including FDA, BAM oxygen service, and LOX mechanical impact sensitivity certifications, DNV-GL.
- Inorganic Filler with Pure PTFE Resins
- Filled PTFE Gasket Material
- ASTM F104: F452111-A9B5E11K6M6
Gasket Factors | 1/16″ | 1/8″ |
---|---|---|
m | 2.2 | 4.6 |
Y, psi (MPa) | 1,937 (13.4) | 1,639 (11.3) |
Gb, psi (MPa) | 639 (4.4) | 495 (3.4) |
a | 0.220 | 0.262 |
Gs, psi (MPa) | 55 (0.379) | 65 (0.448) |
Colour | Blue |
Fiber System | Inorganic |
Temperature Min Max Continuous, Max | -212°C (-350°F) 271°C (520°F) 260°C (500°F) |
Pressure, Max, bar (psi) | 103 (1,500) |
Density, g/cc (lbs/ft³) | 2.2 (138) |
Compressibility, % ASTM F36 | 8-16 |
Recovery, % ASTM F36 | 40 |
Creep Relaxation, % ASTM F38 | 30 |
Tensile Strength, across grain ASTM F152, MPa (psi) | 13.8 (2,00) |
Sealability, cc/min ASTM F2378 (Nitrogen) | 0.01 |
Volume Resistivity, ohm-cm ASTM D991 | 1.0 x 105 |
Dielectric Breakdown ASTM D149, kV/mm (V/mil) | 16 (406) |
Flexibility ASTM F147 | 5x |
Note: ASTM properties are based on 1/16” sheet thickness, except ASTM F38 which is based on 1/32” sheet thickness. This is a general guide only and should not be the sole means of accepting or rejecting this material. The data listed here falls within the normal range of product properties, but should not be used to establish specifications limits nor used alone as the basis of design. For applications above Class 300, contact our technical department